- Particle board is environment friendly material, made of wood particles glued together, like wood chips, flakes, strands, sawdust, and wood shavings.
- They are also called chipboards or low-density fiberboards (LDF).
RELATED VIDEOS
Manufacturing of particleboard
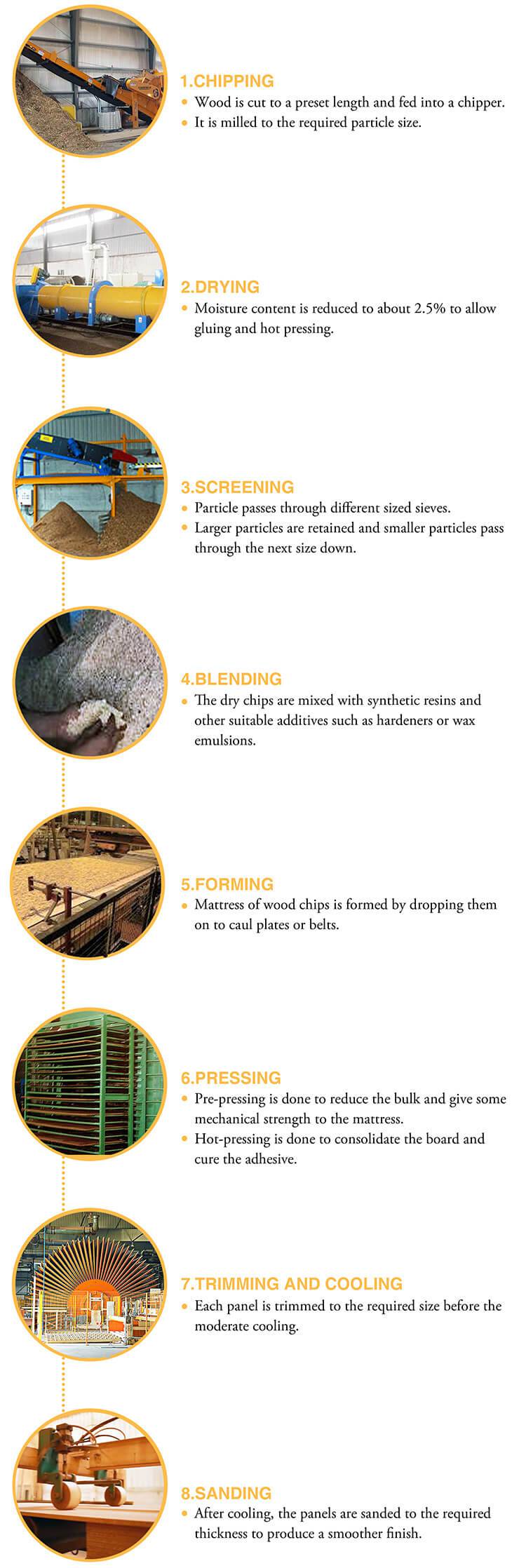
Properties of particle boards
1. Weight and Density
- Being composed of wood residue and wood waste, particle boards are extremely lightweight as compared to MDF or plywood
2. Density
- Their density is greater than natural wood and plywood and lesser than MDF and high density fibreboards.
3. Strength
- They cannot withstand heavy loads as they are made of weak materials.
4. Resistance to Moisture
- Particle boards are vulnerable to moisture. They swell, crack and get discoloured in the presence of moisture.
5. Resistance to Warping:
- Particle boards cannot resist warping.
- Coating them with primer or paint can improve resistance and strength.
6. Durability
- Particle boards are less durable than plywood or solid wood due to their low strength.
- Application of laminates or veneer on the surface helps increase the durability.
7. Insulation
- Particle boards have excellent sound insulation properties, making them suitable for use in recording studios and concert halls.
8. Fire Resistance
- Particle boards can be made fire resistant by attaching a layer of melamine on the top surface.
9. Environmentally-Friendly
- They are eco-friendly materials as they are manufactured from recycled materials and waste like wood chips, wood shavings, sawdust, etc.
General uses of particle board
1. Flooring
- It is used as a flooring material in temporary structures where load application is less.
- Wood veneer particle boards or laminated particle boards are used where a finished aesthetic look is required.
2. Flooring Underlayment
- They are used as a base for parquet flooring, wood flooring or carpets.
- To make them water and termite proof, particle boards are treated with resins and chemicals.
3. Partitions or Wall Paneling
- They are a convenient option for partition walls, being non-load bearing and possessing excellent thermal and sound insulation properties.
- Laminated particle boards are ideal for wall panels.
4. False Ceilings
- Laminated particle boards and cement particle boards are widely used in false ceilings due to their thermo-acoustic insulation character.
- They are used as ceiling tiles for auditoriums, movie theaters.
5. Core Material for Doors
- They have a smooth and flat surface for bonding with the door skin, as well as better screw holding capacity than MDF.
6. Furniture
- Wood veneer particle boards are used as countertops, cabinets, tables, etc.
- Plain particle boards are suitable for beds, storage units, shoe racks, TV cabinets and small shelves.
7. Commercial Industry:
- Particle boards, especially wood veneer particle boards are used in televisions, speaker boxes, sewing machine tops and automobile parts.
Types of particle boards and their uses
Following are the types of particle boards available in markets:
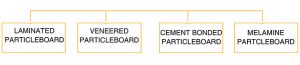
1. Laminated Particle board
- It is manufactured by gluing a thin layer of laminate on the surface of plain particleboard.
- The lamination enhances its appearance and durability.
2. Veneered Particle Board:
- Veneered particle board is manufactured by attaching veneer on the top surface of the plain particle board.
- They have more resistance to warping, because they are properly sealed.
- They replicate the aesthetics of natural wood at lower cost.
3. Cement Bonded Particle Board:
- It comprises 60% cement, wood waste particles like wood chips, sawdust, shavings 20%, wafers and strands.
- This board employs cement as a bonding agent and is moisture, fire and rot resistant.
- It has high expansion and shrinkage properties in humid conditions.
4. Melamine Particleboard:
- Sheet of melamine-impregnated decor paper is glued on top of the plain particleboard under heat and pressure.
- The melamine-urea formaldehyde resin along with wax emulsion provides a strong bond and makes it water resistant.
- These are durable and scratch resistant.
Modifications
Properties such as moisture and fire resistance and acoustic insulation can beenhanced by modifications to produce quality particleboard. For instance:
- Three-layer particle board
- Moisture resistant particle board
- Cement bonded particle board
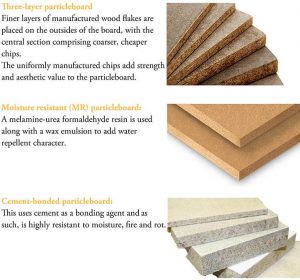
Available sizes and thickness of particle boards
Size:
Inches | Milimeters |
---|---|
8' x 4' | 2449 x 1219 |
Milimeters |
---|
9mm |
11mm |
12mm |
17mm |
18mm |
25mm |
Advantages of particle boards
1. Cost-effective
- Laminated particle boards and veneered particle boards provide aesthetic effects at lower prices than plywood.
2. Lightweight
- Due to this property, they can be handled and transported easily.
3. Easy to maintain
- They do not dent or distort easily. Moreover, they require minimum maintenance and can be cleaned easily
4. Easy to work on
- Particle boards have better screw holding capacity than MDF, so they are widely used to make furniture that can be assembled using screws.
5. Good insulator
- They have thermo-acoustic insulation properties, so are suitably used in speakers and false ceilings in theatre, auditoriums.
6. Eco-friendly
- They use wood waste such as wood chips, sawdust, wooden shavings, and bagasse (residue of sugarcane after the juice is extracted).
Disadvantages of particle boards
1. Low strength
- They can be easily damaged during transportation due to their low density. They cannot support heavy loads.
2. Easily damaged
- They expand and warp. Discoloration may occur under extreme conditions.
3. Not durable
- They have shorter lifespan compared to MDF and plywood due to their lower strength and damage by moisture.
4. Toxic
- They are manufactured using urea formaldehyde resin which is the source of formaldehyde gas. The resin may break down and release the toxic gas even after many years of installation, which is carcinogenic for humans i.e. causing cancer.