RELATED VIDEOS
Classification of rocks

1. Geological Classification:

2. Physical Classification:

3. Chemical Classification

Properties of good building stones
1. Appearance and Colour
- Stone must be of good appearance and uniform in colour
- Stones light in colour resist weathering action better.
2. Crushing Strength
- The crushing strength of stone should be greater than 100 N/mm2.
- Rock preference on the basis of Crushing strength: Igneous rocks > Metamorphic rocks > Sedimentary rocks
Rock |
Stone |
Crushing strength in N/mm2 |
Igneous | Granite | 75 - 140 |
Sedimentary | Limestone Sandstone | 55 65 |
Metamorphic | Marble Slate | 70 - 75 70 - 210 |
3. Weight
- Good quality building stones possess heavy weight to resist higher compressive forces.
- Good quality building stones must have a specific gravity greater than 2.70.
- A heavy stone is more compact and less porous.
Stone |
Specific Gravity g/cm3 |
Granite | 2.6 - 2.7 |
Limestone | 2.3 - 2.7 |
Marble | 2.4 - 2.7 |
Sandstone | 2.2 - 2.8 |
Shale | 2.4 - 2.8 |
Slate | 2.7 - 2.8 |
Quartzite | 2.6 - 2.8 |
4. Hardness and Toughness
- The stones must be hard and tough to resist wear and tear (Coefficient of hardness should be greater than 17).
- Hardness is assessed by scratching and toughness by hammering.
- A good quality building stone possesses wearing resistance less than 3% , if greater than 3%, it is not satisfactory.
High Scratch Resistance |
Medium Scratch Resistance |
Low Scratch Resistance |
Granite Quartzite | Basalt Sandstone | Schist Marble Slate Limestone |
5. Porosity and Absorption
- The presence of pores causes rainwater to percolate, which damages the stone.
- A good quality stone should not absorb water greater than 0.6% by weight.
- It must resist atmospheric effects. If stones in cold climates absorb water, they may freeze and cause the stones to split.
Type of Stone |
Maximum Limit of Water Absorption (%) |
Granite | 1 |
Limestone | 10 |
Quartzite | 3 |
Sandstone | 10 |
6. Compactness
- A good quality stone must possess a compact, fine, crystalline structure.
- A compact, strong stone better resists the effects of external agencies.
- For example: Granite, Marble,etc.
7. Fineness of Grain
- Stones are ideal for moulding and are easily carved and dressed.
- Non-crystalline structured stones get damaged under the action of natural agencies.
- For example: Sandstone, Gneiss ,etc.
8. Fire Resistance
- Stones must not undergo deformation when subjected to fire.
- Limestone resists fire up to about 800 °C.
- Sandstone is better resistant to fires.
- Despite having poor strength, argillaceous stones like Slate and Laterite are highly fire resistant.
9. Durability
- Building stone must possess high durability.
- Durable stones are compact, homogeneous, acid resistant and have negligible water absorption.
10. Dressing
- Dressing of stones requires them to be soft and have uniform texture.
- For example: Granite, Marble , etc.
General uses of stone
Common building stones are used for the following purposes:1. General Building Works
- In foundations, walls, superstructure (columns, arches, lintels, roofs, floors, damp proof courses etc.) and composite masonry.
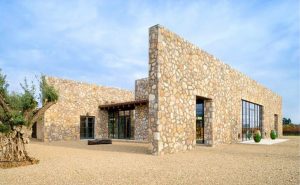
2. Buildings Exposed to High Wind
- In areas subject to high winds, for instance, near the sea, stone structures will be subject to weathering.
- Hence, stones possessing high crushing strength and silica presence in addition to hardness are preferable.
- Granite and Basalt can be used.

3. Heavy Engineering Works
- Heavy engineering works include docks, harbours, bridges, piers, abutments, retaining walls etc.
- Quartzite is generally preferred for such purposes.

4. Road Metals and Railway Ballast
- Road metals and railway ballasts are subject to high compression & abrasion and are exposed to external agencies throughout their life.
- Stones selected for such purposes should be hard, tough and highly abrasion resistant.
- Quartzite and Basalt are generally preferred.
5. Facing and Architectural Items
- Facing slabs and stones, landings and staircase parts, parapets and guard rails are made of slabs sawn or split from natural stone.
- Sandstone, Slate and Marble are used for these purposes.
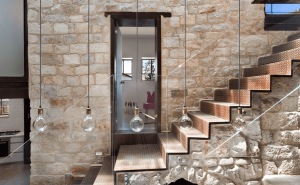
Quarrying of stone
- Quarrying is the process by which stones are extracted from the surface of the earth.
- Quarry is the place from where the stone is obtained.
1. Quarry Location
Prior to quarrying, the quarry location is decided on the basis of:

2. Methods of Quarrying
a) Digging
- In case of soft rocks, stones are extracted by digging with simple hand tools such as pick-axes, hammers, chisels, etc.
- Only those stones that occur in the form of detached nodules buried in the Earth can be practically quarried by this process.
b) Heating
- This method is used to separate the upper layer of rock by burning fuel, mostly wood.
- Due to burning for several hours, unequal expansion of the rock occurs, and the rock gets separated from the cold mass with a dull noise.
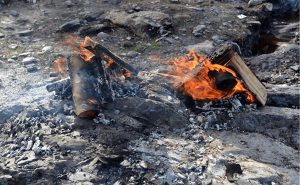
c) Wedging
- Soft stratified rocks can be removed by wedging as these rocks are in the form of layers and split easily.
- Soft rocks are removed with the help of pick axes and crow bars. Limestone, marble, slate and laterite are removed by this method.
d) Blasting
- Quarrying of hard and compact rocks is carried out by this method
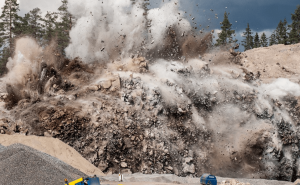
Natural stone finishes
1. Natural cleft
- This finish cannot be created, but occurs naturally as the layers are quarried.
- Some marbles, granites and limestone are available with natural clefting, suit able for wall installations or paving purposes only.
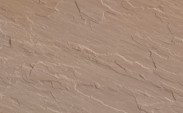
2. Tumbled
- This finish simulates aging and generates soft surfaces and edges.

3. Honed
- This finish is a satin smooth surface with little light reflection.
- This is best for low maintenance, high traffic applications.

4. Brushed
- The roughness of the surface is formed by means of metal brushes that take away the softest particles of the stone.
- The stone tile is not slippery and looks a bit worn-out.

5. Polished
- Grinding, sanding, and buffing produce a high gloss, mirror-like surface.
- The most popular uses of polished stone are in; interior and exterior wallcladding.
- It is not recommended for outdoor paving, since it reduces slip resistance.

6. Bush hammered
- This finish is created by hitting the material, manually or mechanically, with a bush hammer which generates uniformly distributed craters.
- The surface becomes non-slip, ideal for high traffic external areas.

7. Sandblasted
- This finish is achieved by repeatedly blasting silica sand against the material through an air gun to the stone's surface.
- This is rough and have tidy look.

8. Leather
- This finish is obtained by a process of brushing the slab with a range of brushes.
- This texture is smooth and slip-resistant.

9. Flamed
- This finish is achieved by exposing the surface of the stone directly to a high temperature flame.
- This is used where slip resistance is a concern.

10.Water blasted
- A high pressure jet of water is applied to the stone surface in order to wash out the softer particles.
- The surface is less slippery.

11.Split Face
- This finish is achieved by splitting stone either by hand or by machine so that the surface exhibits a natural quarry texture.
- It has a flat back and uneven front surface, and creates the uneven look of protruding bricks.

Natural stone prices
- Customizing stone slabs causes wastage and thus an increase in prices.
- The cost depends primarily on the finishes.
- The price increases for Hand cut; machine cut and finished stones respectively.
Durability of stone
Stone durability is dependent on the environment in which it is used. Stones with exposed faces are exposed to various atmospheric and external agencies.
1. Deteriorating Agencies of Stones
Various factors are responsible for deterioration of stones. They are dis cussed below:
- Alternate wetness and drying
- Frost
- Atmospheric impurities
- Movement of Chemicals
- Living organisms
- Rain Water
- Nature of mortar
- Temperature changes
- Vegetable Growth
- Wind
2. Climatic effects
- Stones such as generic sandstones are avoided in exteriors because of their high porosity
- They absorb water and get degraded through change in appearance.
- To counter this, chemical weather proofing is done.
- The water absorption capacity of Limestone, quartzite and granite is relatively less than sandstone.
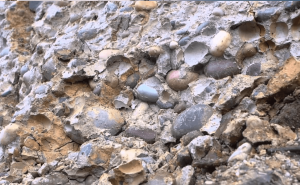
Common building stones in india

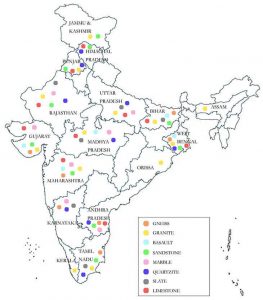
Preservation of stones
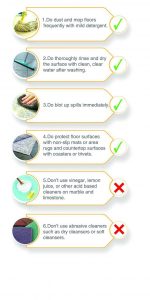
Artificial stones
- Artificial stones also known as cast stones or reconstructed stones composed of cement, sand, and natural aggregate such as crushed stone.

Artificial Stone Mix Ratio
Types of Artificial Stones
1. Cement Concrete Blocks
- These are manufactured using cement, fine aggregate, coarse aggregate and water similar to that of concrete.
- Sometimes, they are precast with steel and are therefore called reinforced cement concrete blocks.

2. Artificial Marble
- It is made combining sand with Portland cement or one of the gypsum or magne site cements.
- It is either precast or cast-in-situ and is used for external work.

3. Terrazzo
- It is prepared using mixtures of marble chips with white cement and some pigment.
- It is also either precast or cast-in-situ.

4. Mosaic Tiles
- These are precast tiles in which the top surface consists of marble chips.
- These are available in various sizes and colours.
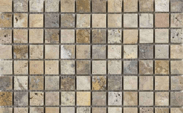
5. Bituminous Stone
- Diorite and other granite stones are soaked with prepared or refined tar to form bituminous stones.
- These stones are used where noise-proof, wear-proof & dust-proof surfaces are needed.

6. Reconstructed Stone
- This is made from the debris of lime stone quarries by crushing them into grit.

Advantages of Artificial Stones
The advantages of artificial stones are as follows:
- Any required size and shape can be attained easily.
- In areas where natural stones are expensive and unavailable, artificial stones are used.
- Can be made on-site and thereby the cost of dressing the stone and transport can be saved.
- They are free of defects when compared with natural stones.
- Cavities can easily be made in artificial stones for wiring or plumbing work.
- Better against deterioration & disintegration caused by various at mospheric agencies.
- It is comparatively more durable than natural stones.
Limestone
- Limestone is a rock of sedimentary origin, composed mainly of calcium carbonate or dolomite or both.
- The primary source of the calcite in limestone is most commonly marine organisms.
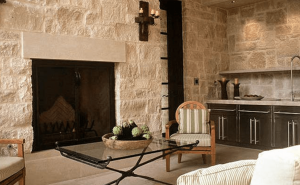
PHYSICAL PROPERTIES OF LIMESTONE
Physically, Limestone is quite impervious, hard and compact, mostly exhibiting granular texture.
1. Crushing Strength
- Varies from 50-240N/mm2.
2. Hardness and Toughness
- It lies between 3 - 4 on the Mohsscale of mineral hardness.
3. Weight
- The specific gravity varies from 2.20 to 2.60.
4. Porosity and Absorption
- The capacity of water absorption is less than 1.0%.
- It has low porosity.
CHEMICAL PROPERTIES OF LIMESTONE
Composition |
Percentage |
Silica (SiO2) | 20-25% |
Aluminum oxide (Al2O3) | 2 to 4% |
Lime(CaO) | 38% to 42% |
Other Oxides like Na, Mg | 1.5% to 2.5% |
Loss On Ignition(LOI) | 30% to 32% |
GENERAL USES OF LIMESTONE IN CONSTRUCTION
1. Masonry Construction
- In the construction of load bearing walls, monuments and retaining walls.
2. Structural Applications
- Used in constructing canopies, arches & domes of various sizes and forms.
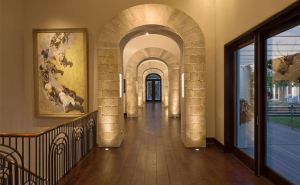
3. Interior Applications
- Limestone can be used for flooring as well as wall cladding.

4. Outdoor Applications
- Limestone is used in construction of wells, fountains and water channels.

FORMS OF LIMESTONE
1. Limestone Slabs
- Ideal to be used in commercial and residential places for flooring purposes.

2. Limestone Tiles
- Limestone being a soft stone isextremely versatile and can easily be cut into various sizes and shapes.

3. Blocks
- Limestone blocks are available in different sizes and are used for constructing retaining walls, garden edging, etc.
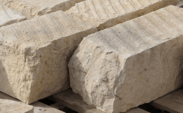
ADVANTAGES OF LIMESTONE
1. Versatility
- Limestone has a warm neutral color tone and also comes in a variety of colors and size.

2. Durability and Dependability
- Limestone has a great natural durability.
- The Great Pyramids were built using limestone.

3. Carving
- Limestone is a somewhat soft rock form; it can also be easily shaped and hand carved.

4. Cost Effective
- It is cheaper and therefore more economically viable than many other building materials such as marble.
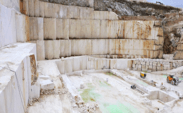
DISADVANTAGES OF LIMESTONE
1. Porous and Soft
- It is a soft stone, it can discolor and scratch easily and can cause permanent staining.
- It is also vulnerable to acid and other chemical effects.

- Quarrying of limestone is more expensive than using a different building material that requires a less invasive extraction process.
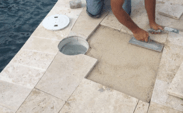
- Health problems such as asthma arise on the quarry site from the increased levels of dust in the air.

Sandstone
Sandstone is a sedimentary rock composed of sand-sized grains, naturally cemented by mineral particles of very small size (0.0625 to 2 mm).

SANDSTONE COMPOSITION
The main constituents of sandstone are two minerals that are the most abundant ones in the Earth's crust, i.e., feldspar and quartz.
SANDSTONE PHYSICAL PROPERTIES
1. Appearance and Colour
- Sandstone is found in grey, dark grey, red, buff, brown & yellow shades.
- The variation is result of the binding material and its percentage constituent.
2. Compressive Strength
- Varies from 20 to 170 N/mm.
3. Weight
- The specific gravity varies from 2.2-2.8.
4. Hardness and Toughness
- Lies between 6-7 on Mohs Scale.
5. Porosity and Absorption
- The water absorption capacity is not more than 1.0%.
- The porosity varies from low to very low.
SANDSTONE CHEMICAL PROPERTIES
They are highly resistant to acids, alkalis and thermal impact.Chemically, Sandstone are composed of:
Composition |
Percentage |
Silica (SiO2) | 93-94% |
Aluminum oxide (Al2O3) | 1.4 to 1.5% |
Iron(Fe2O3) | 1.5%-1.6% |
Lime(CaO) | 0.8% to 0.9% |
Soda(Na2O) & Potash (Kro) | 1.0% to 1.2% |
Loss On Ignition(LOI) | 1.0% to 1.2% |
Magnesia(MgO) | 0.2 to 0.25% |
GENERAL USES OF SANDSTONE
1. Masonry construction
- Used for Load bearing masonry, foundations, etc

2. Architectural work
- Use for stonewalls, flooring and cladding.

3. Decorative purposes
- Used to enhance aesthetics.
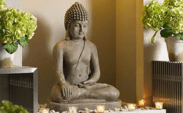
4. Outdoor applications
- Easy to carve so used for making pillars, arches, pavements, garden furniture, fountains, landscaping products as well as stone arts & crafts.

FORMS OF SANDSTONE
1. Sandstone slabs
- Sandstone slabs are used for gardens, kitchens, living rooms, etc.

2. Sandstone tiles
- Sandstone tiles are mostly used for flooring & wall cladding.

3. Sandstone cobbles
- Sandstone cobble stones can be used for garden landscaping, paving, decorative purposes, etc.

4. Sandstone pebbles
- Sandstone pebbles are used as decorative stone in homes, artificial ponds, fountains, gardens, etc.
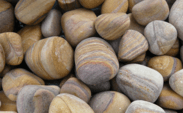
5. Sandstone strips
- Sandstone strips are used for indoor areas as well as decks, patios, or as swimming pool surrounds.

6. Sandstone bricks
- Sandstone bricks are widely used for the purpose of paving, cladding, boundary wall construction, etc.

SANDSTONE SIZES AND THICKNESSES
Sizes
Sandstone size in Sq.ft |
Sandstone size in mm |
1.5 X 2 | 400x600 |
2 x 2 | 600x600 |
2.6 x 2.6 | 800x800 |
2.6 x 2.6 | 1200x600 |
Thickness
ADVANTAGES OF SANDSTONE
1. Versatile
- Sandstone covers ranges in colour from medium white all the way back to charcoal and black.

2. Durability
- Sandstone is strong enough to last for decades if properly cared.

3. Uniqueness
- Every individual unit of sandstone possesses a unique colour, pattern and texture.

4. Replaceable
- Sandstone flooring is installed in individual tiles or pieces, the tiles can be removed and replaced with relative ease.

DISADVANTAGES OF SANDSTONE
1. Water absorption
- Sandstone can have an absorption rate of between 1-6 percent, which leaves it vulnerable to damage from liquid stains, moulds, micro-bacteria, and even warping in extreme cases.
- For this reason it is generally not preferred in damp areas.

2. Slippery when wet
- Polished sandstone can be a particularly dangerous slipping hazard, especially in areas where water may be present.

3. Weathering with age
- Sandstone is too soft to resist general wear and tear and deteriorates under atmospheric effects.

Slate
- Slate is a fine-grained, foliated, homogeneous metamorphic rock derived from an original shale-type sedimentary rock.
- It is composed of clay or volcanic ash formed through low grade metamorphic process.

SLATE COMPOSITION
PHYSICAL PROPERTIES OF SLAT
1. Appearance and colour
- The colour varies from black, blue, green, grey, purple or red.
- Colour changes may occur due to weathering.
2. Compressive Strength
- Varies from 24 to 36 N/mm.
3. Hardness and Toughness
- Slates are usually soft and can be easily scratched.
4. Weight
- The specific gravity varies from 2.7-2.8.
5. Absorption
- The water absorption capacity is less than 1.0%.
CHEMICAL PROPERTIES OF SLATE
- Chemically they are Multi-Mineral, metamorphic argillaceous rocks made of an aggregate of minerals and colloidal substances.
- It is fairly resistant to acids and staining.
Composition |
Percentage |
SiO2 | 55-65% |
Iron (Fe2O3) | 4%-8% |
Alumina (Al2O3) | 15 to 20% |
Soda (Na2O) & Potash (K2O) | 2-4% |
Lime (CaO) | 0.5-1% |
Magnesia (MgO) | 0.5-3% |
TiO2 | 0.4-0.5% |
Loss On Ignition (LOI) | 3-4% |
GENERAL USES OF SLATES
1. Architectural work
- It is used for flooring, wall cladding, roofing etc.

- It is used for making sculptures.

FORMS OF SLATE
1. Slate stone Slabs
- The building industry employs the use of slate stone slabs for roofing purposes, gravestones, snooker tables, & Slate stone slabs.

2. Slate stone Tiles
- Slate stone tiles are used in wall-cladding, roofing and flooring.

3. Slate stone Blocks
- Slate stone blocks are quarried stones used to create fireplaces, hearths, gravestones, etc.

4. Slate stone Strips
- The highly durable slate stone strips find application in wall cladding, roofing and flooring.

ADVANTAGES OF SLATE
1. Looks prestigious
- Slate exhibits aesthetic beauty, and provides rich shades of black, grey and charcoal colours.

2. Durability
- Slate has an inherent durability that makes it resistant to cracks, scratches, breaks, fire and chips.

3. Replaceble
- It is also possible to repair its pieces to restore the surface with relative ease.

4. Low maintenance
- Slate requires less maintenance than granite or marble.
- It is also non-porous, which allows it to be cleaned easily.

DISADVANTAGES OF SLATE
1. High Cost
- It is very expensive to make and install.
2. Skilled labour
- Slate installation may require expert craftsmanship in certain situations.
Quartzite
- Quartzite is a hard metamorphic rock which was originally quartz-rich sandstone.

QUARTZITE COMPOSITION
- Quartzite is a hard metamorphic rock which was originally quartz-rich sandstone.
- It is created when sandstone underground is exposed to heat, pressure and undergoes metamorphism.
PHYSICAL PROPERTIES OF QUARTZITE
1. Appearance and colour
- Quartzite is unique with its variety of patterns and bright, vibrantcolours.
2. Crushing strength
- Varies from 50 to 300 N/mm.
3. Weight
- The specific gravity varies from 2.6 to 2.8.
4. Hardness and Toughness
- This stone is highly resistant to wear and tear.
- Lies between 6 to 7 on Mohs scale of mineral hardness.
5. Porosity and Absorption
- Quartzite exhibits porous nature with average water absorption of between 0.1 and 1.4%.
CHEMICAL PROPERTIES OF QUARTZITE
- It is made primarily of silica.
- It is highly resistant to fire and anything acidic.
GENERAL USES OF QUARZITE
1. Indoor applications
- Its used for kitchen countertops.
- It is a decorative stone and used to cover walls, as roofing tiles, as flooring, and stair steps.

2. Outdoor applications
- It stands up against abrasion in pool decks, cladding etc.
- Parking lots, driveways and pathways can be grated and topped with quartzite stone.

3. Miscellaneous
- It is often used as railway ballast.
- Crushed quartzite is oftenly used in road construction.

FORMS OF QUARTZITE
1. Quartzite Slabs
- The slabs are put in further use for kitchen countertops.

2. Quartzite Tiles
- Quartzite tiles are mostly used for flooring, walls cladding, shower walls and as roof tiles.

3. Quartzite Mosaic
- Quartzite mosaic is generally used for flooring, cladding and pool decks.

4. Stepping Stone
- The stepping stones find usage in pavements, driveways, etc.

ADVANTAGES OF QUARTZITE
1. Resilience
- Quartzite covers a wide range of varieties resembling marble, and hence is a great substitute.

2. Durability
- Quartzite is resistant to etching and scratching, stands up to heat.

3. Low maintenance
- It is easy to keep clean and sanitized.
- Soap and warm water will make the surface look fantastic.

4. UV resistant
- Quartzite is highly resistant to UV rays, which makes it useful for an out door setting or in a room that gets ample daylight.

DISDAVANTAGES OF QUARTZITE
1. Skilled labour
- The slabs are heavy and should always be cut and installed by a professional.
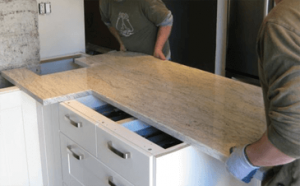
2. Sealing
- Sealing should be done once a year, but there are varieties that need it more often.

3. Limited colour choices
- Quartzite has a limited range of colours, whites and greys are predominant with some shades in between.
- It offers limited options for countertops, compared to granite.
